An meinem WBX im Bus hat sich leider ein Auslassventil verabschiedet, keine Kompression mehr auf diesem Zylinder, das Ventilspiel lässt sich nicht mehr einstellen.
Daher will ich 2 eingelagerte Köpfe zerlegen, reinigen und die Ventile neu einschleifen. Anschließend will ich die Köpfe gegen die verbauten austauschen. Die Ventilsitze und die Ventilführung will ich nur prüfen. Bei Verschleiß werde ich diese natürlich tauschen.
Die erste Herausforderung ist die Demontage der Ventilfedern, der WBX hat pro Ventil zwei davon. Ich hab viele Rezessionen zu Ventilfederspannern gelesen, oft wird geschrieben, dass sich das Werkzeug schon beim ersten Einsatz verbiegt. Getestet habe ich nachfolgende Werkzeuge:
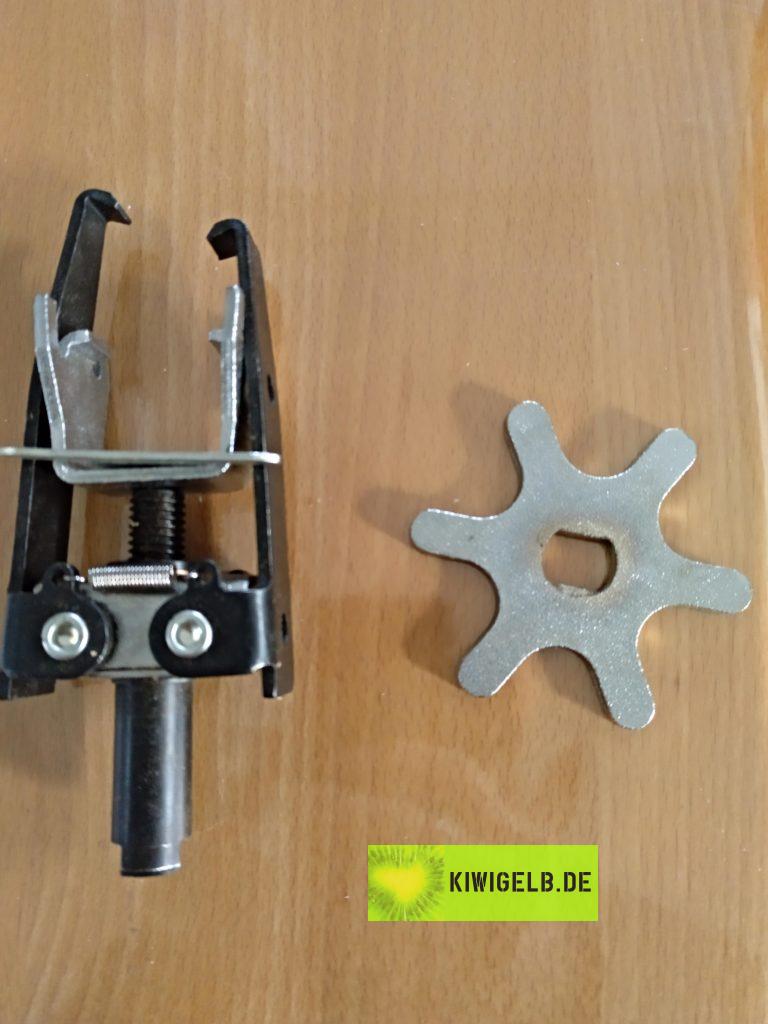
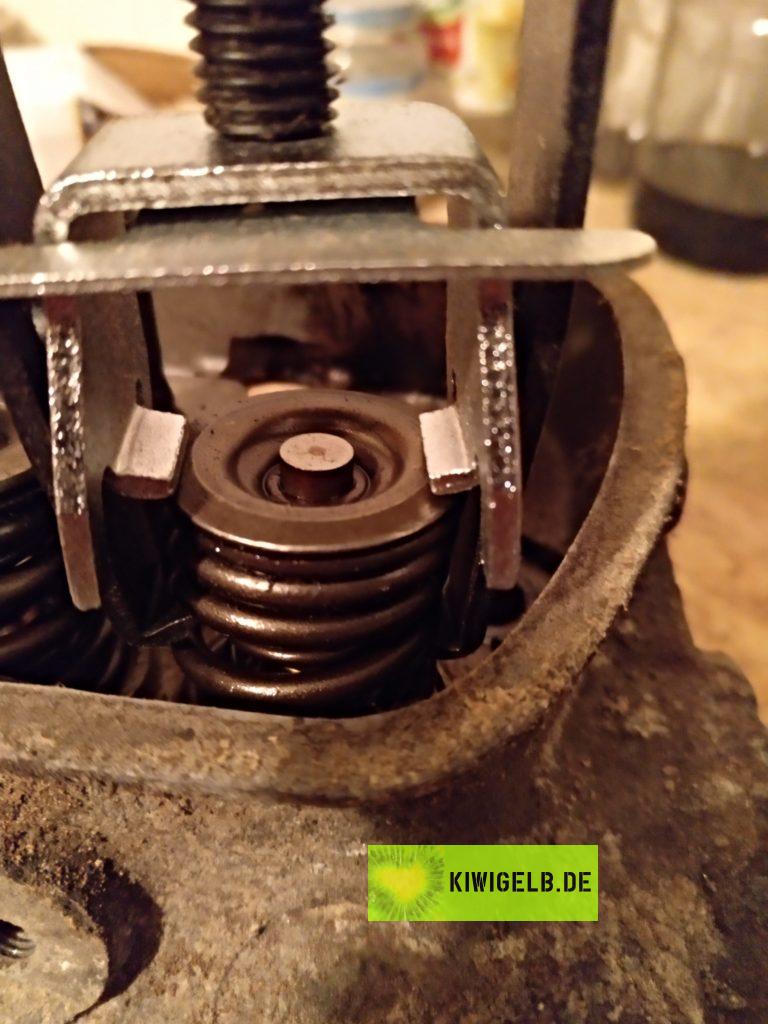
Mit einem selbstgebauten Werkzeug von einem befreundeten Busfahrer klappt es dann wunderbar.
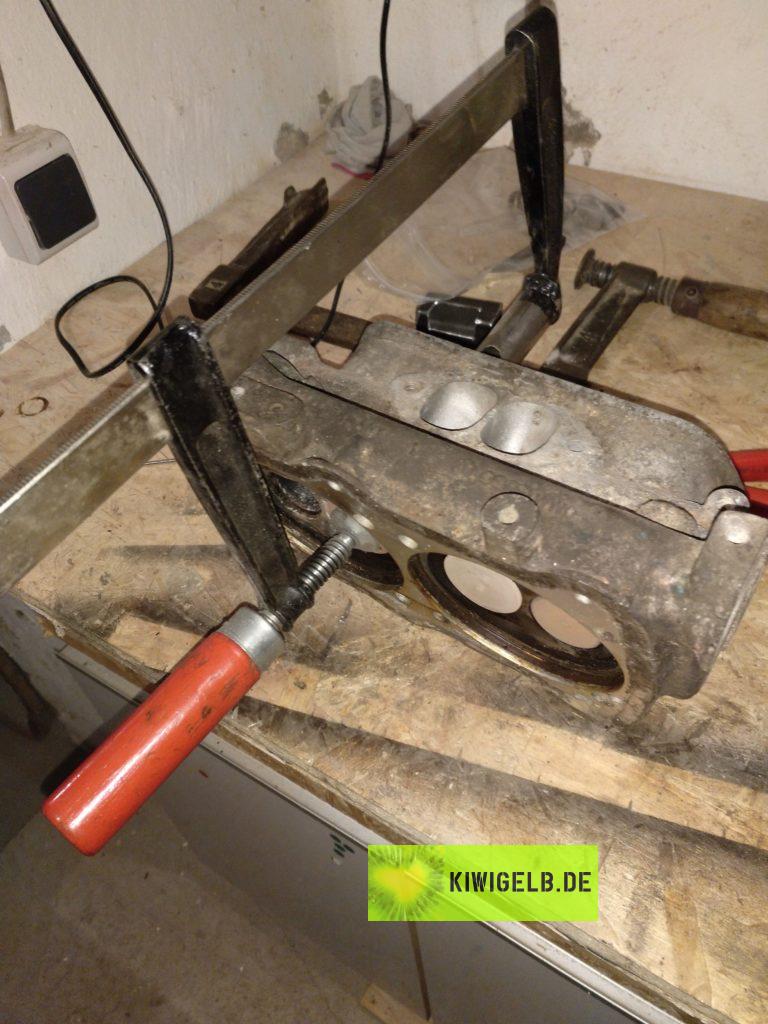
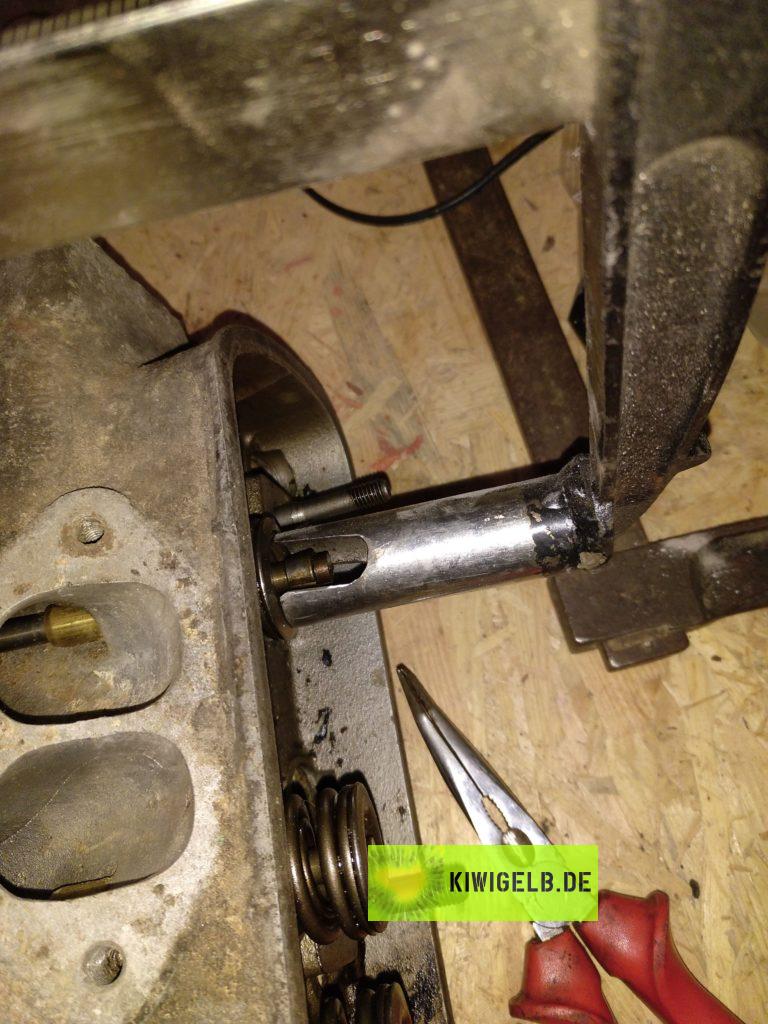
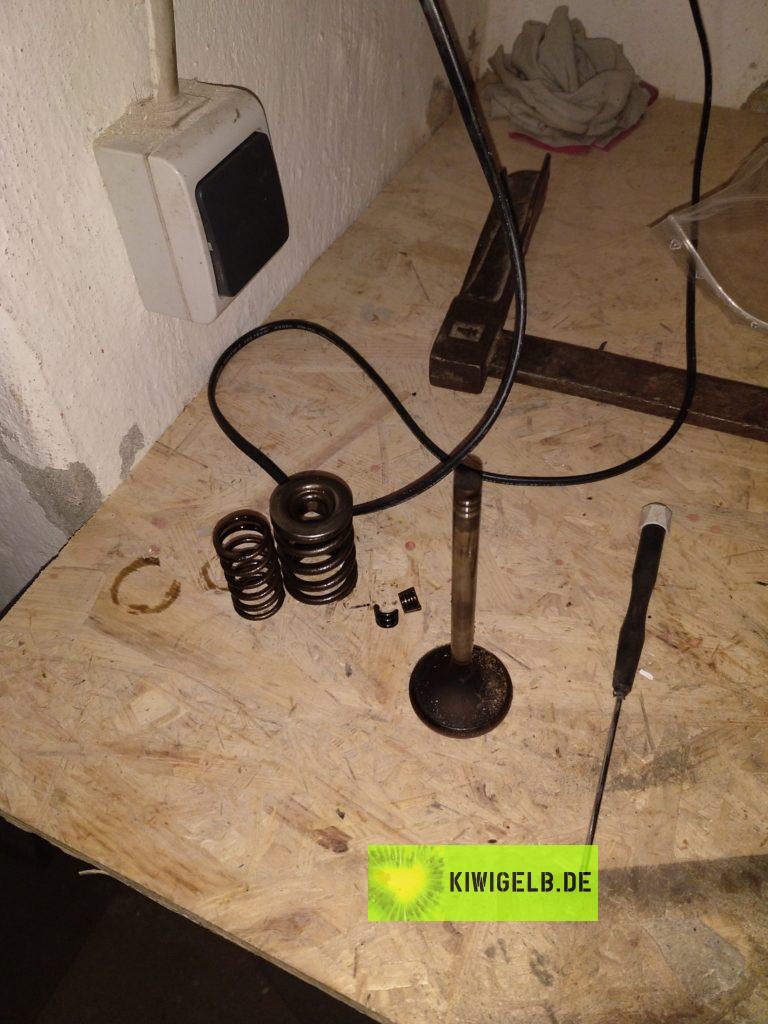
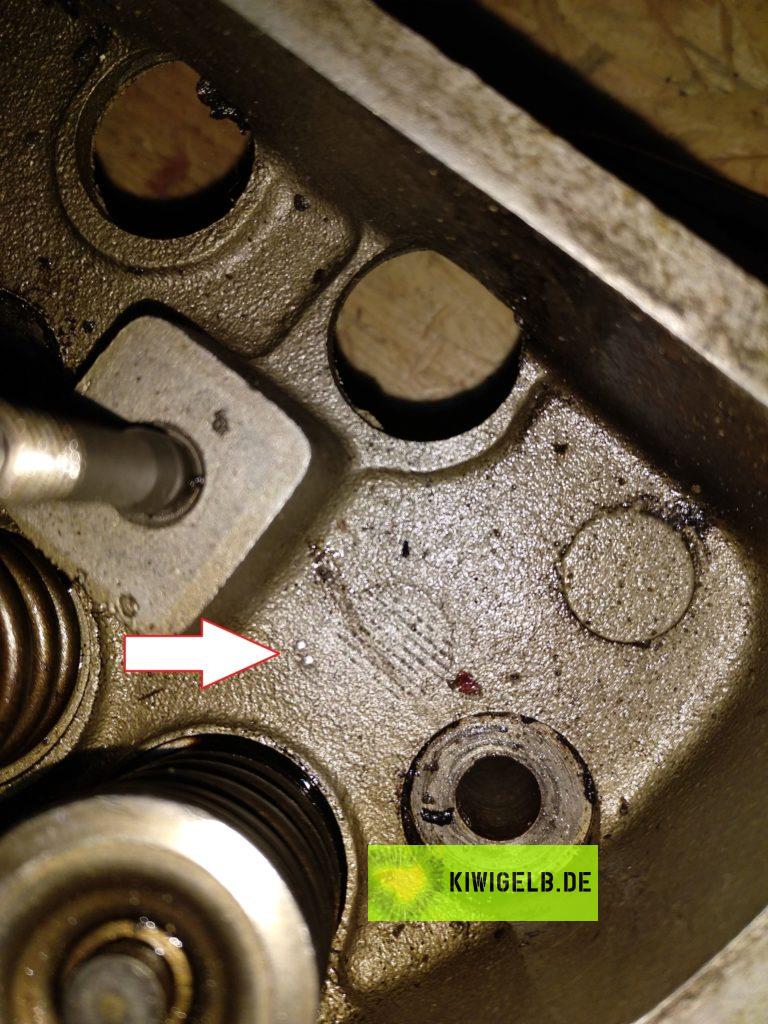
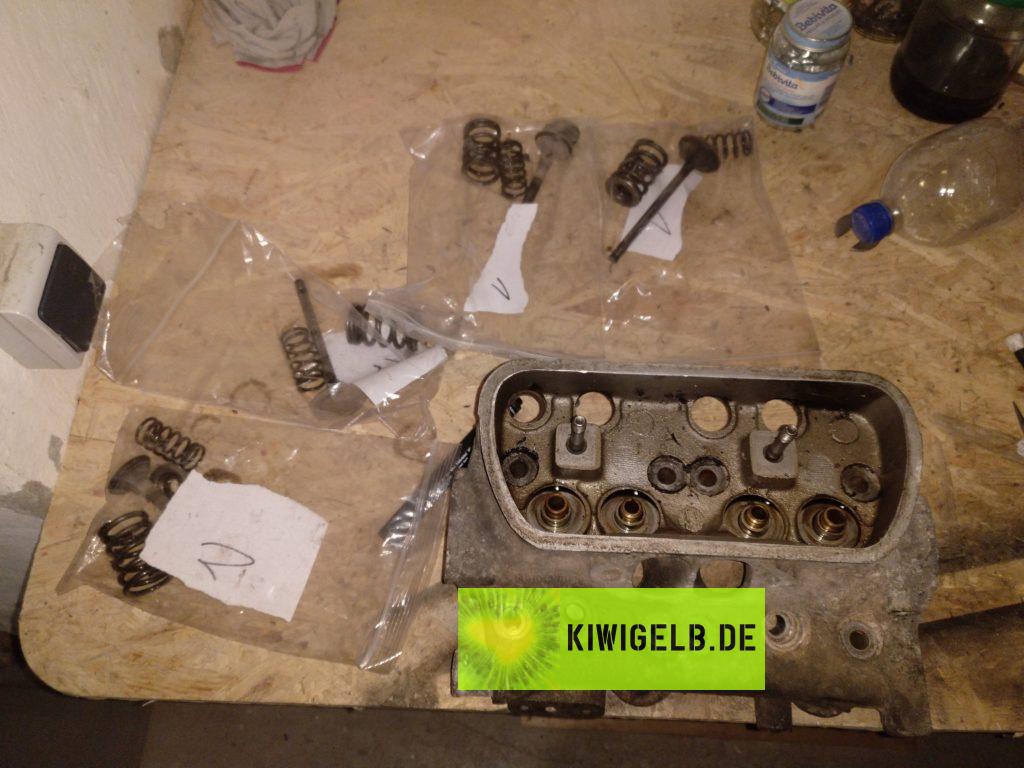
Mit einem Zopfbürstenset bin ich den verdreckten Köpfen vorsichtig zu Leibe gerückt. Gerade bei den Dichtflächen lieber langsam und behutsam vorgehen.
Auch wenn Messing dran steht, es sind eigentlich immer Stahlbürsten mit Messingoptik, erkennt man erst wenn man die Rezessionen liest. Messing wäre schöner aber Stahl geht wohl auch.
Das Ergebnis ist natürlich nicht so schön wie beim Glasperlenstrahlen. Aber man erkennt den Unterschied.
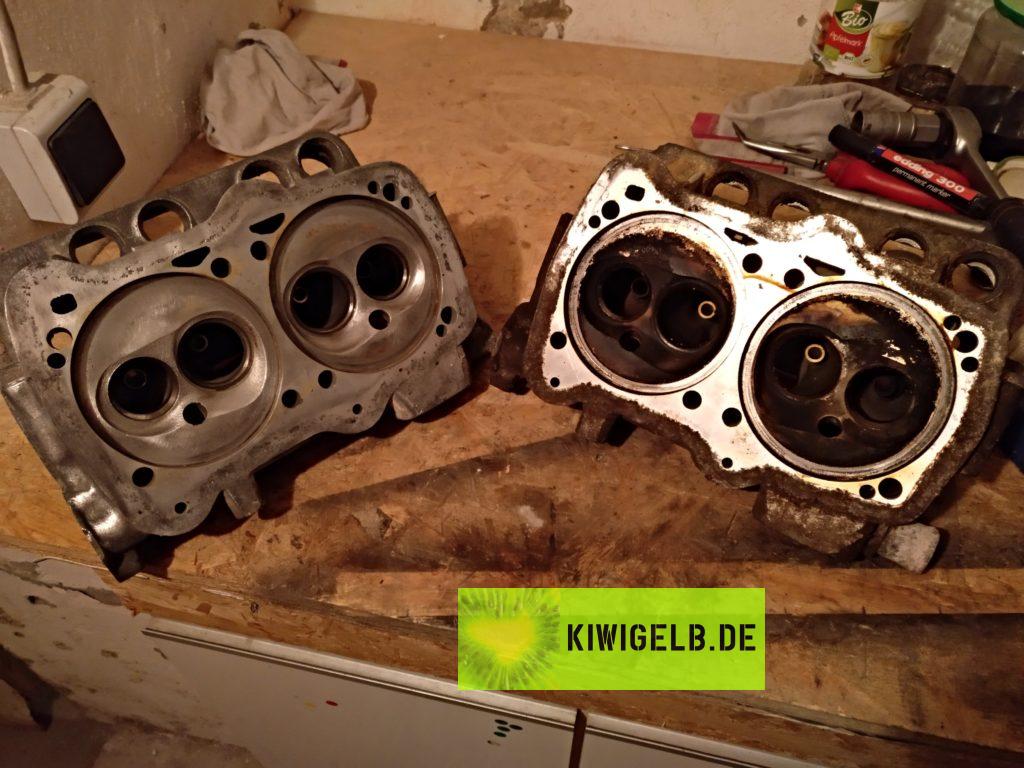
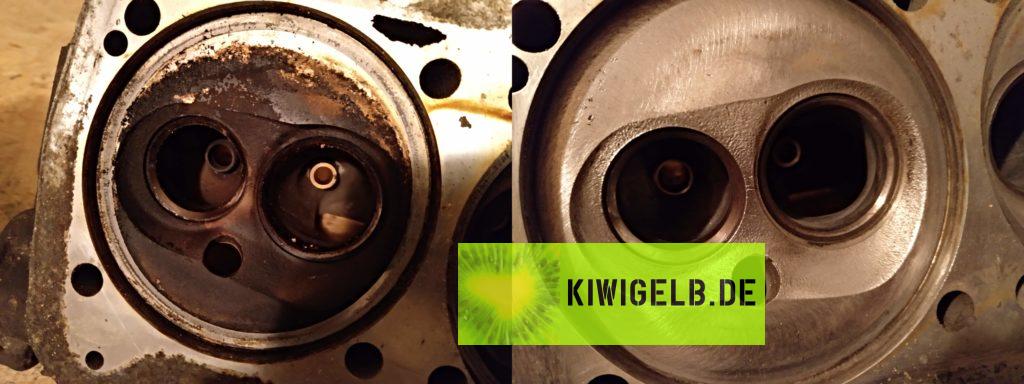
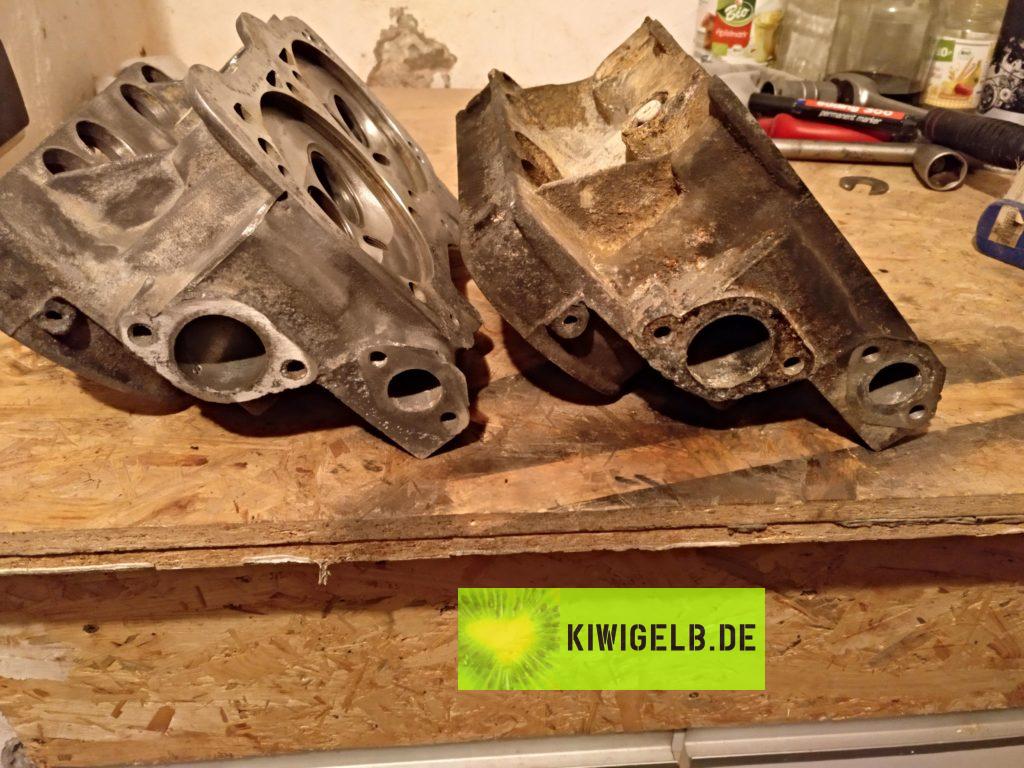
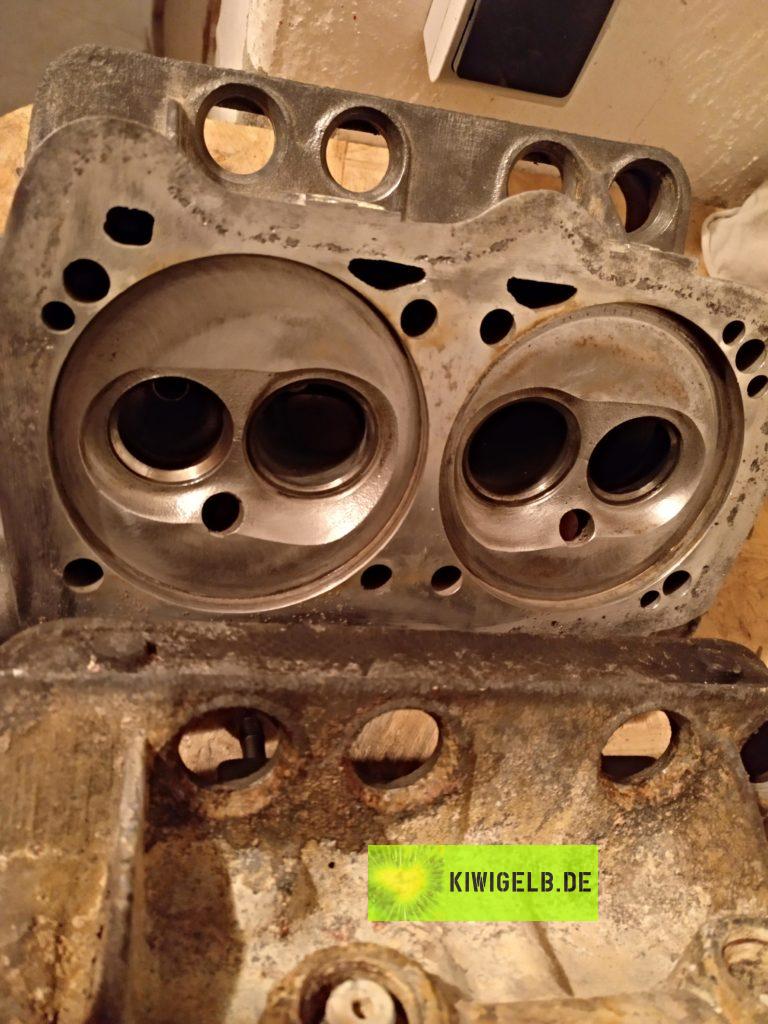
Nun werden alle Gewinde nachgeschnitten und dann werde ich die Köpfe nochmal in einem Reinigungsbecken reinigen.
Der nächste Schritt war das nachschneiden aller Gewinde. Dazu sind nötig:
M8 und M6 Gewindebohrer und M14x1,25 (Zündkerzengewinde)
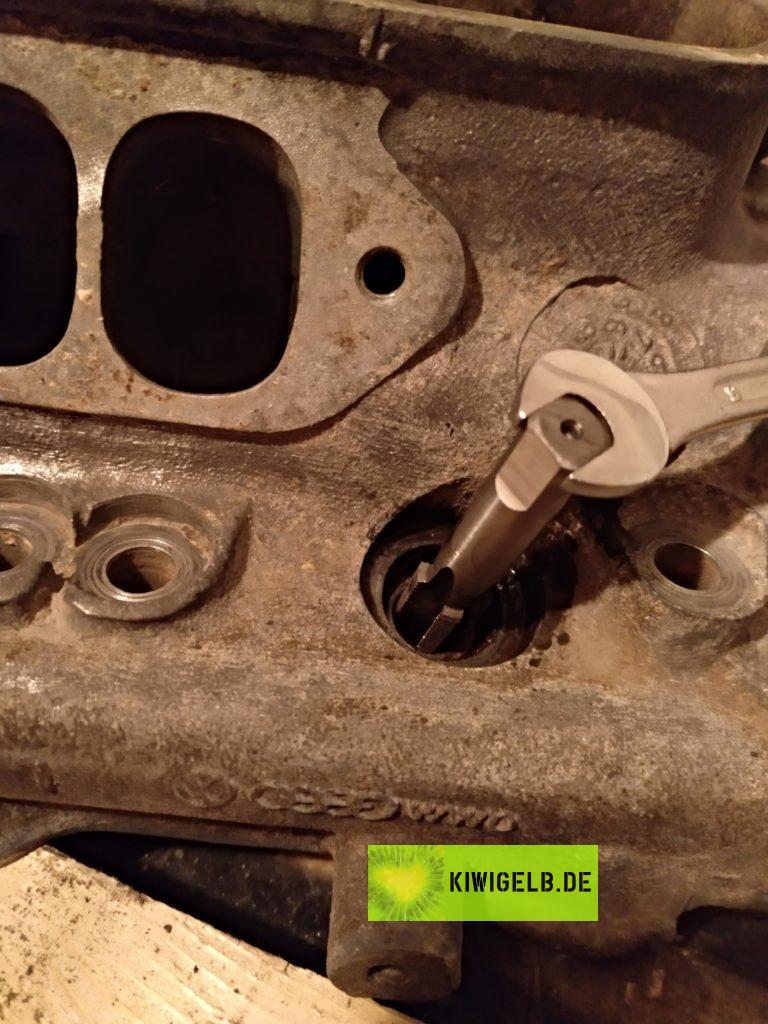
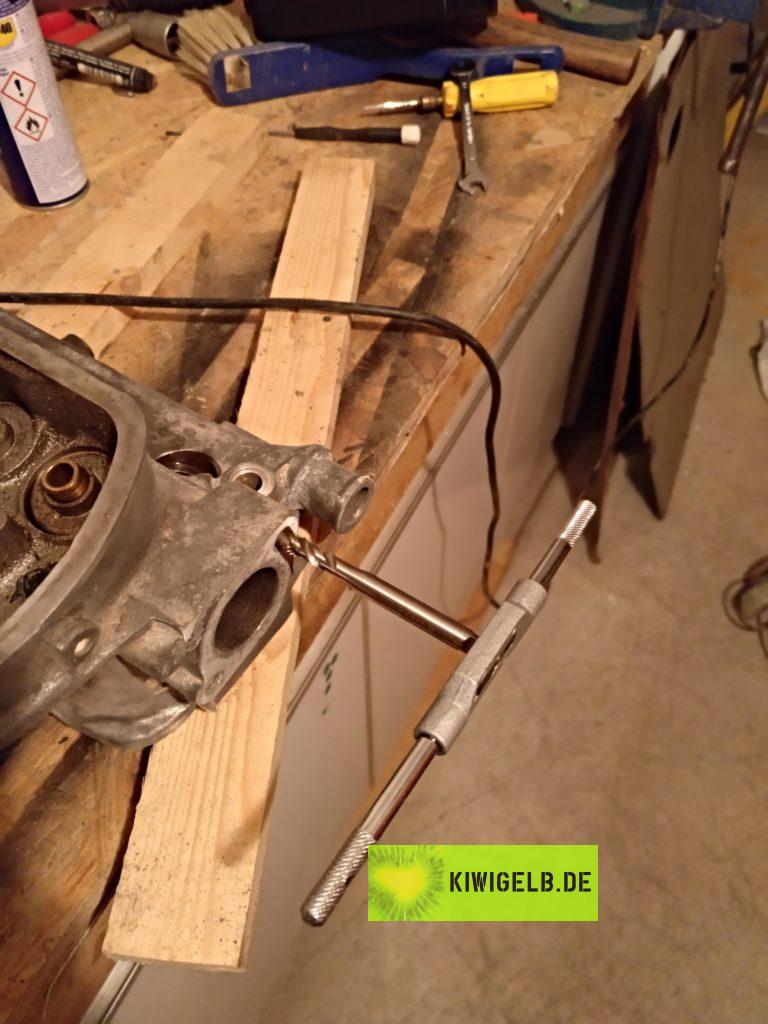
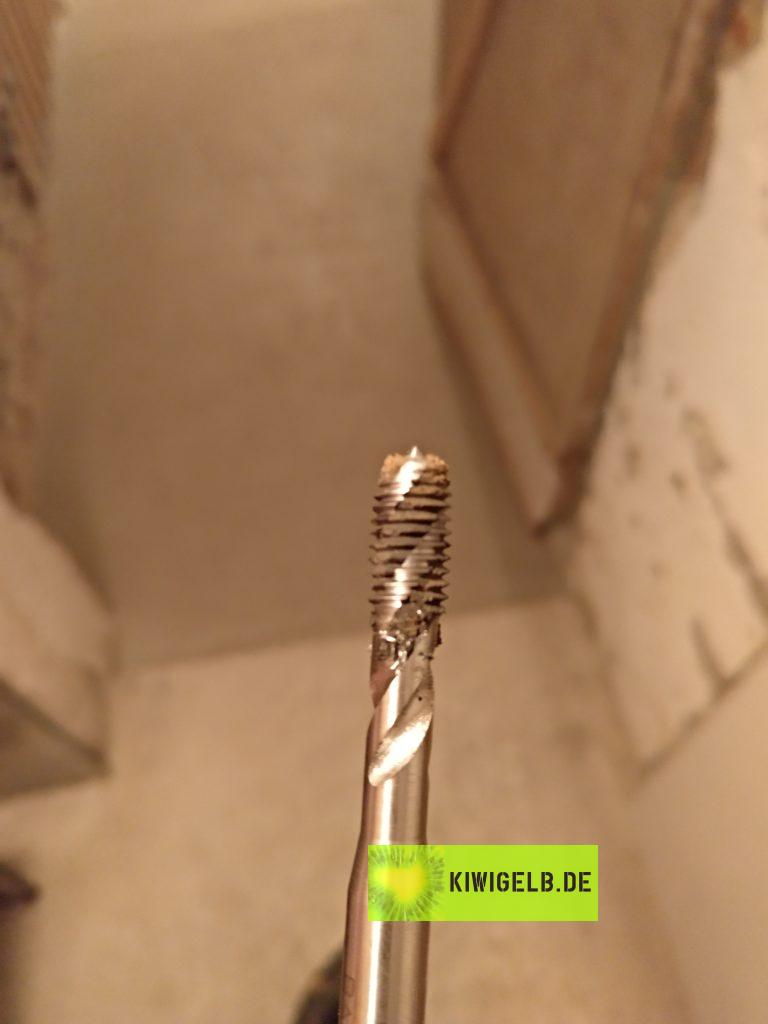

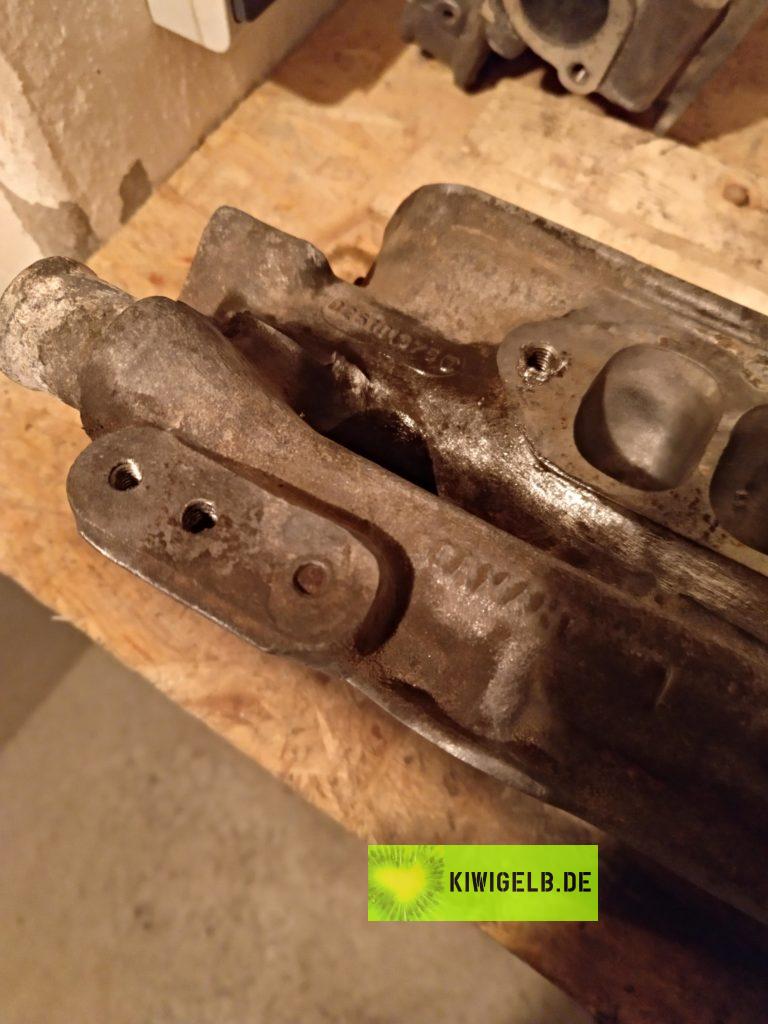
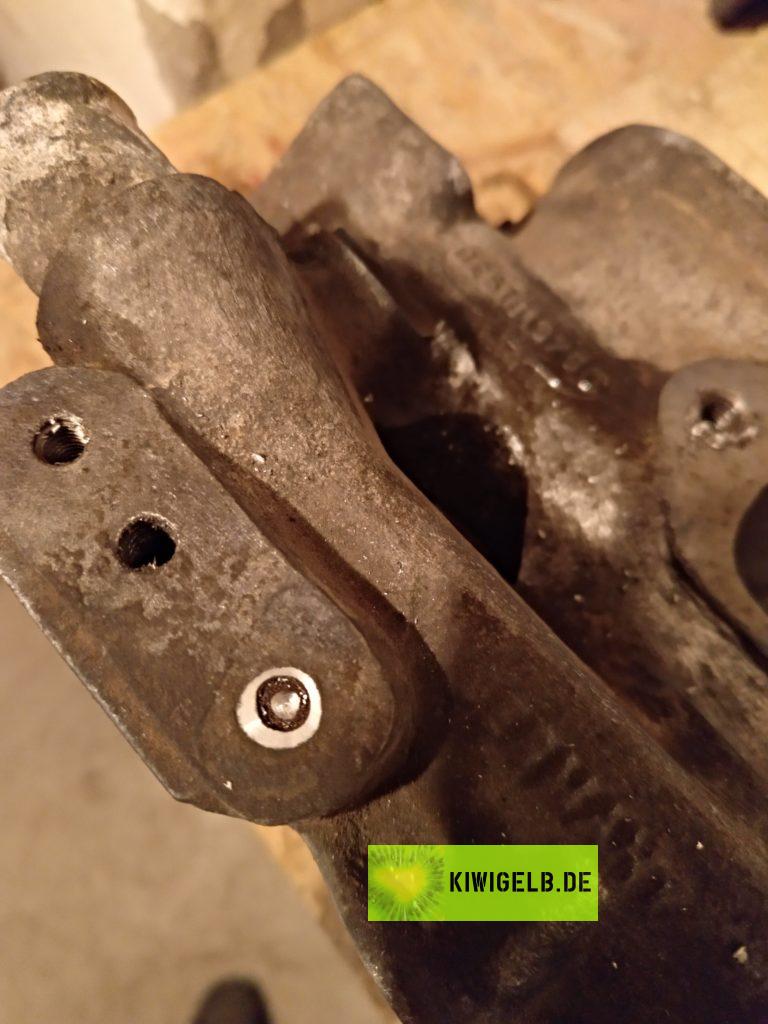
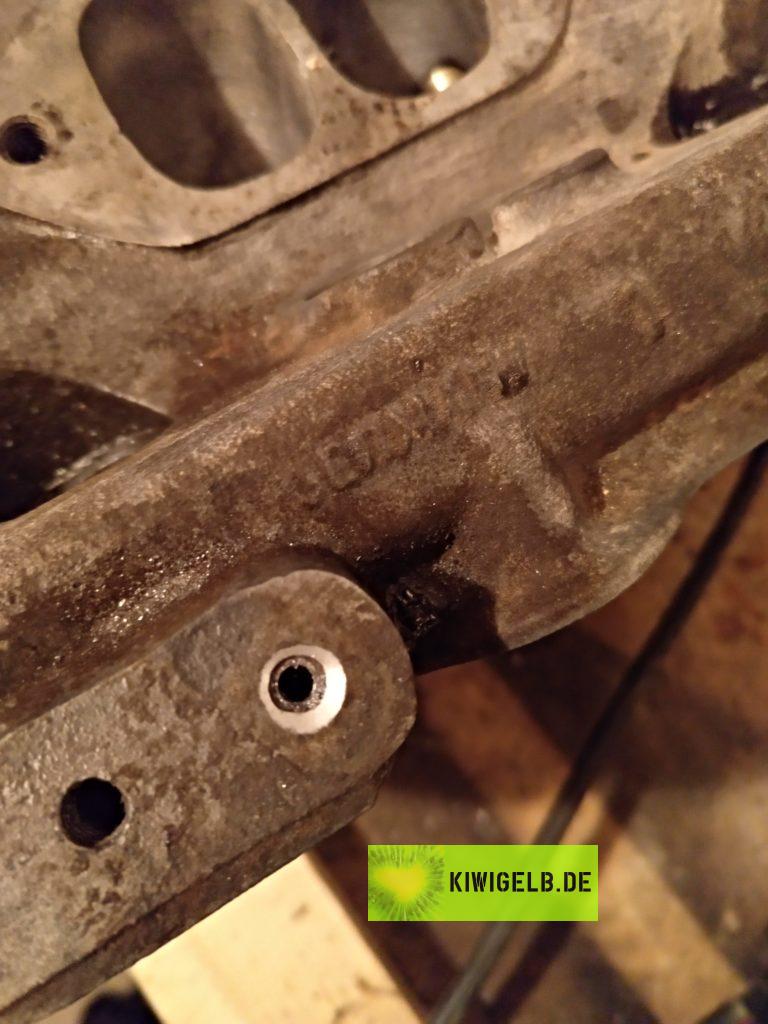
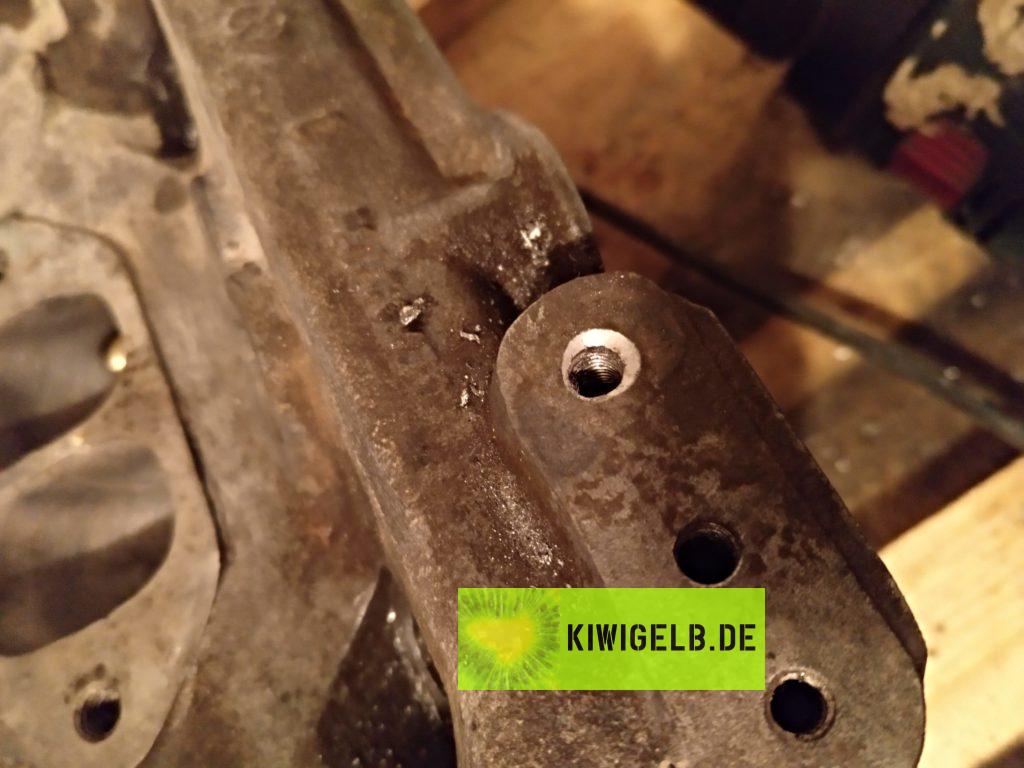
Planen der Flansche. Normalerweise macht dies eine Fräse. Nur hat die wohl keiner daheim. Mit einem Handschleifer geht das auch ganz gut, man sollte nur darauf achten schön plan zu schleifen.
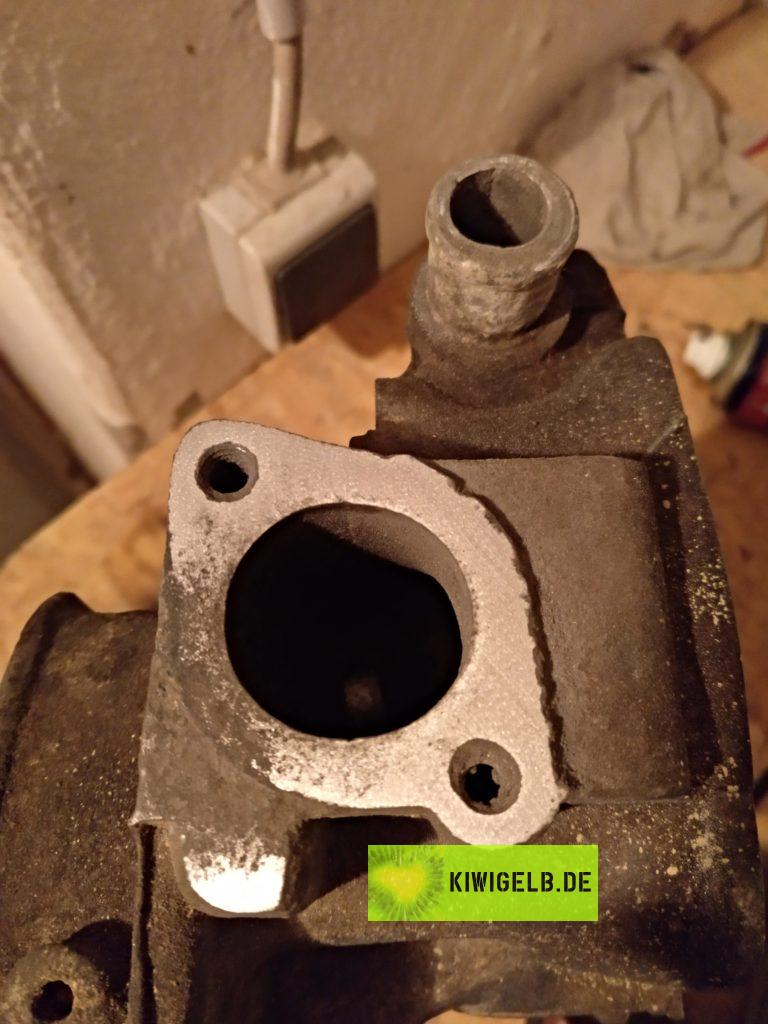
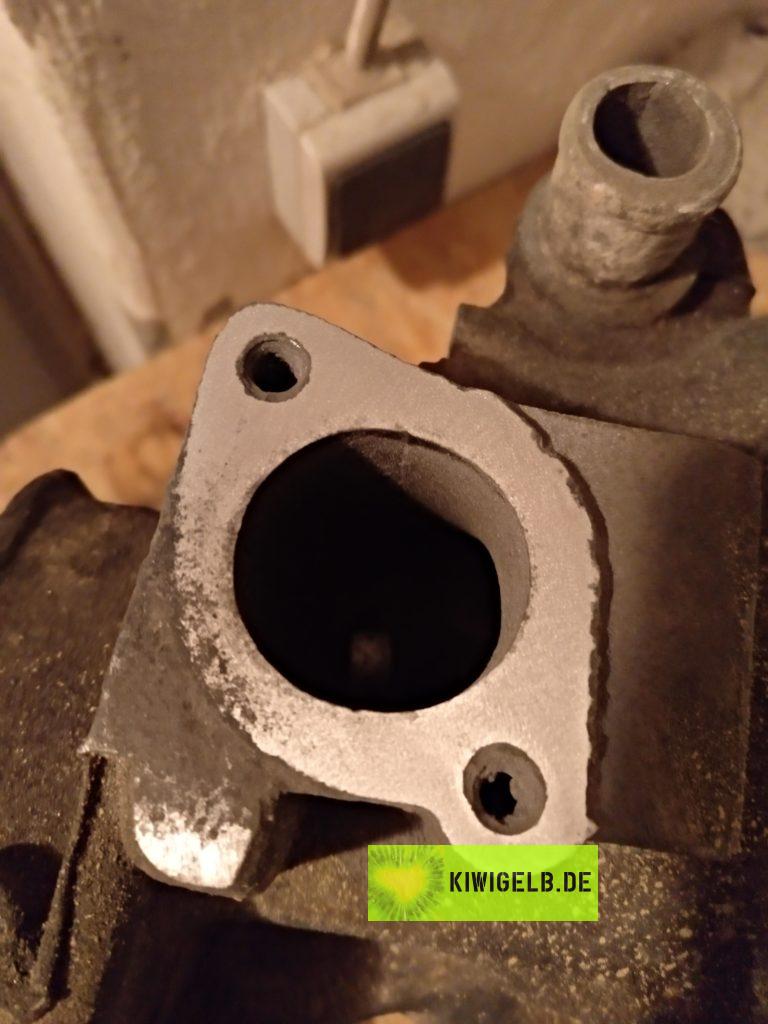
Weiter geht es mit den Ventilen. Auch die habe ich vorsichtig mit den Bürstenaufsätzen bearbeitet.
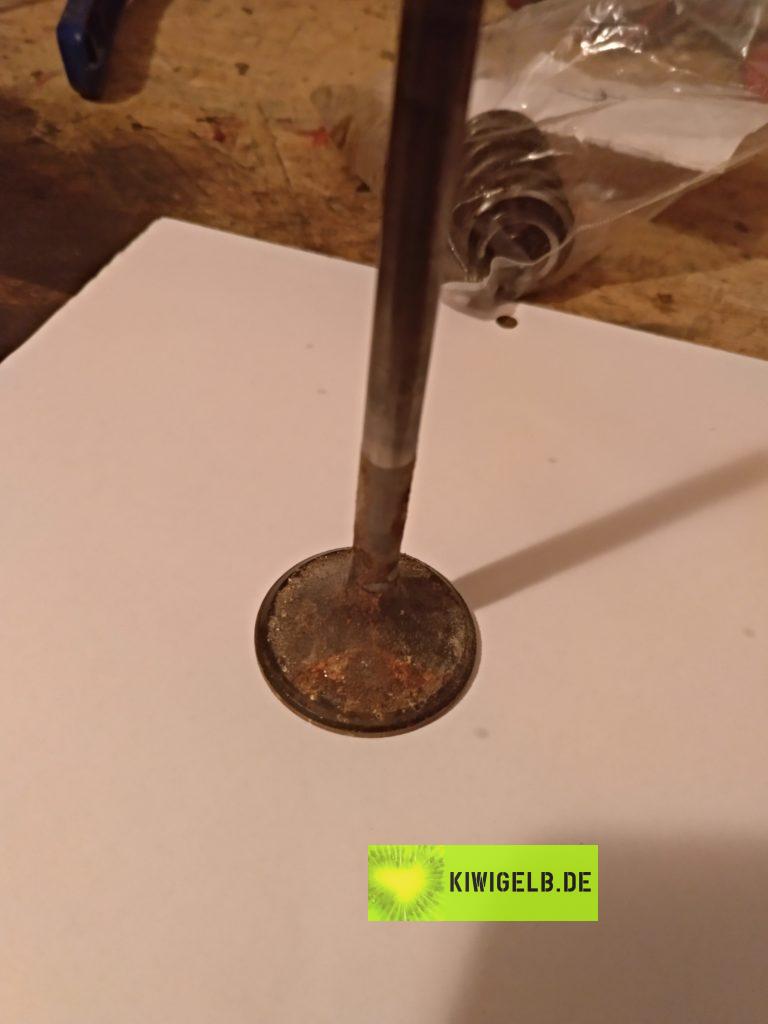
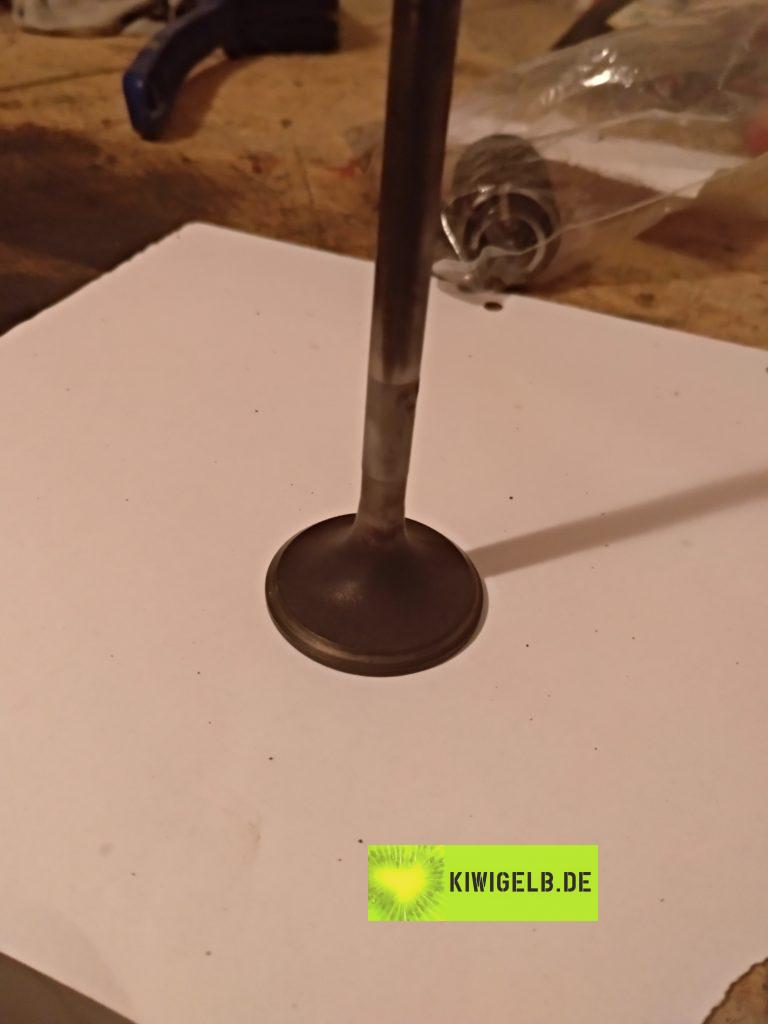
Als nächstes habe ich das Spiel der Ventile in der Ventilführung gemessen. VW gibt als Verschleißgrenze 1,2mm an. Alle meine Ventilführungen lagen unter 0,8mm und dürfen daher drin bleiben.
Es gibt dazu ein passendes VW Werkzeug, welches ich natürlich nicht habe. Daher fix selbst was gebaut.
Zuerst ein Flachstahl mit M8 Gewinde, dieser kann dann am Kopf befestigt werden.
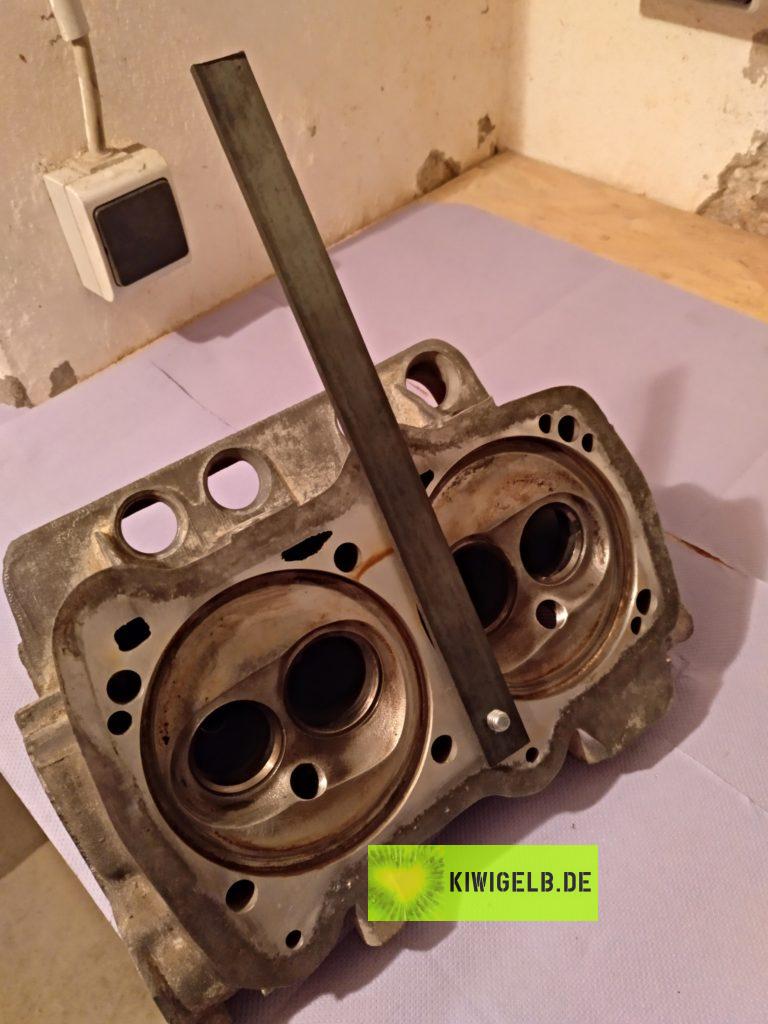
Auf den Flachstahl dann eine Messuhr mit Magnethalter und Gelenkarm montieren.
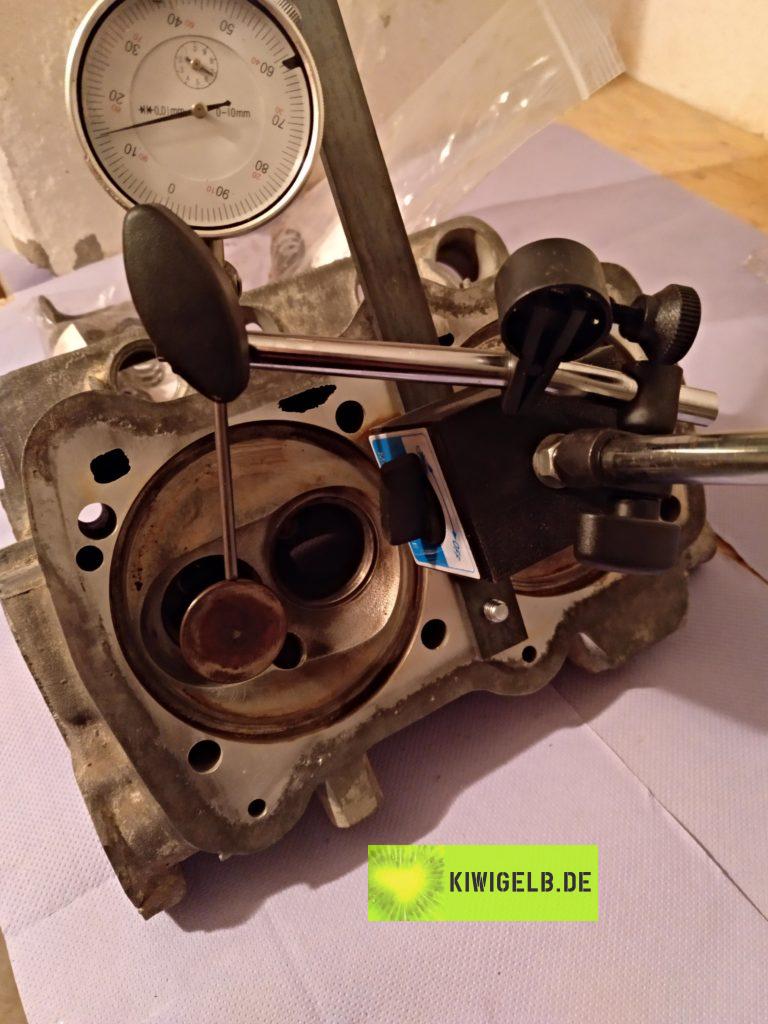
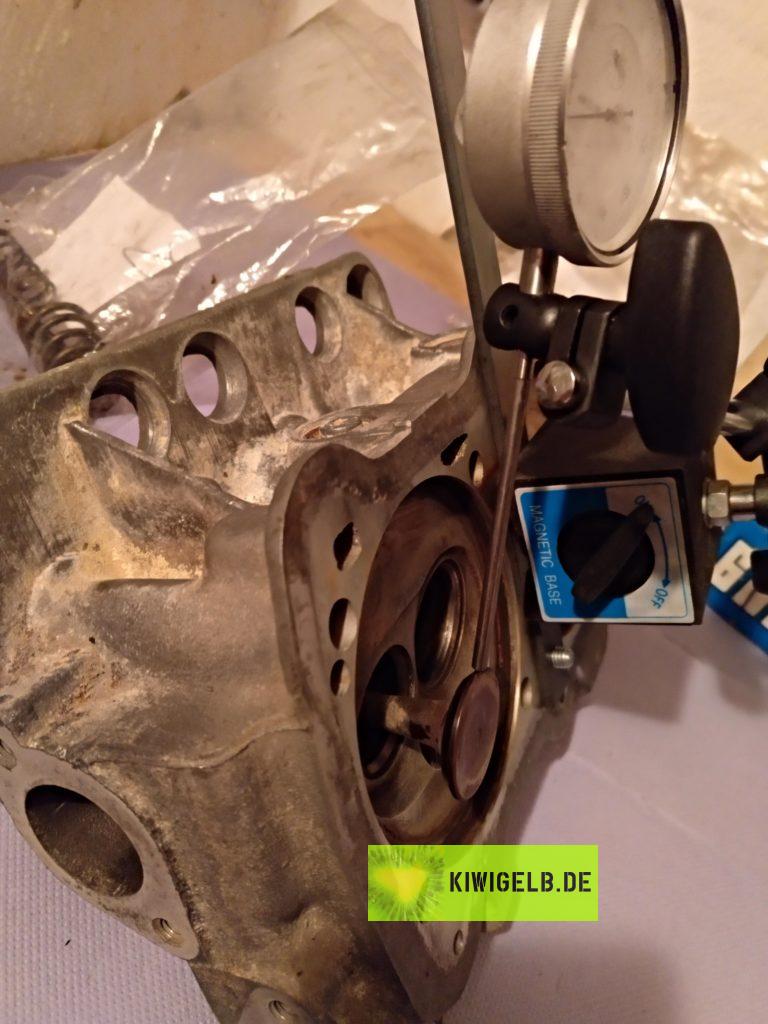
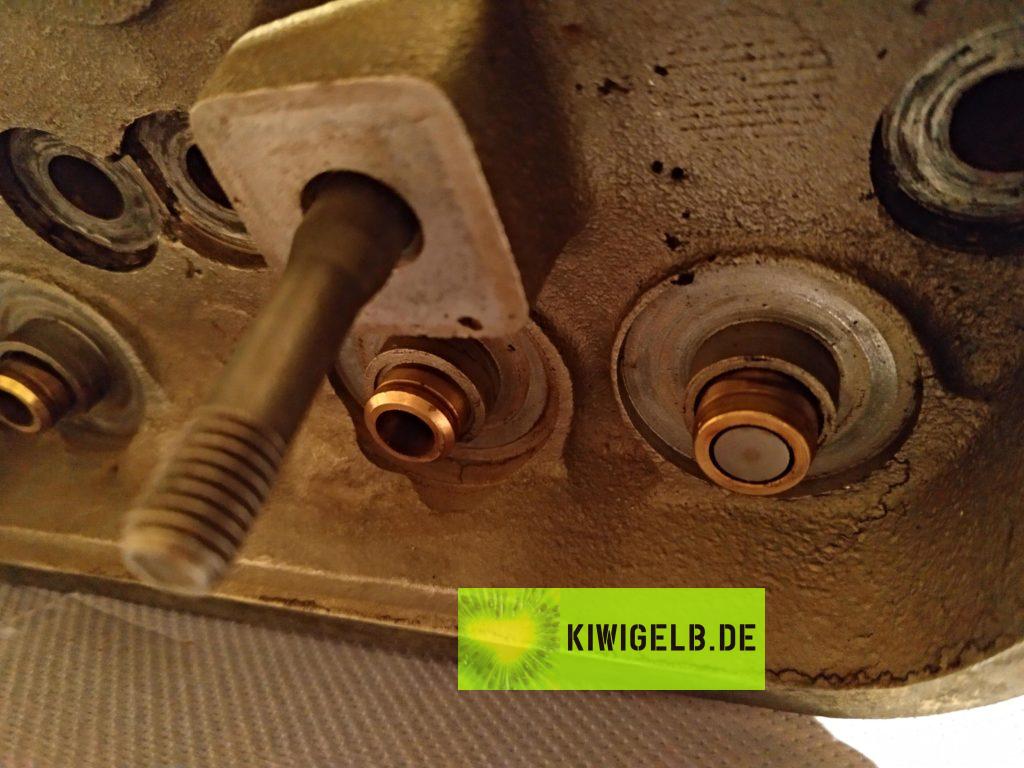
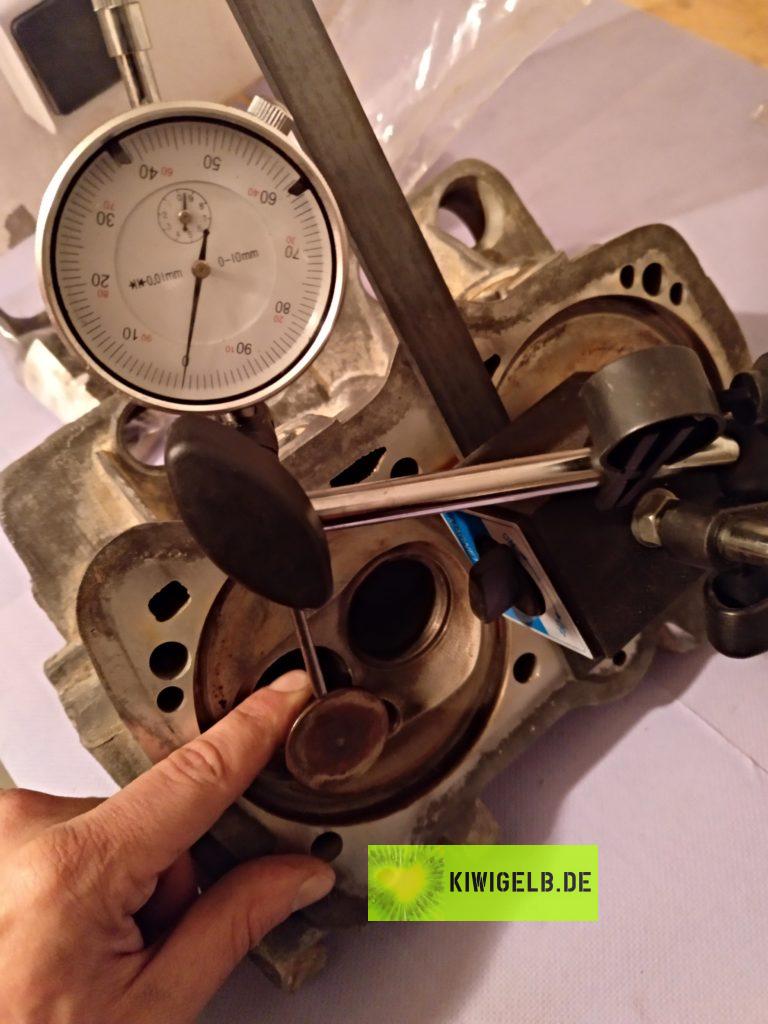
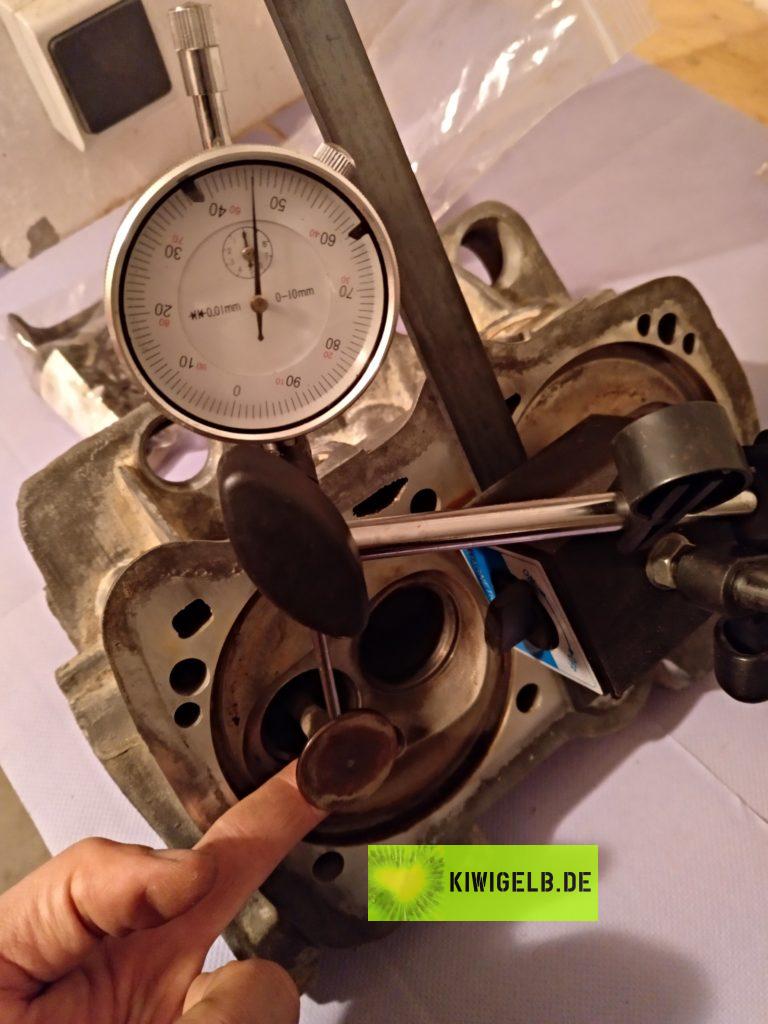
Die Differenz ist das Spiel, im Bilderbeispiel 0,55mm
Der nächste Schritt war das Einschleifen der Ventile.
Hierzu habe ich folgendes bestellt:
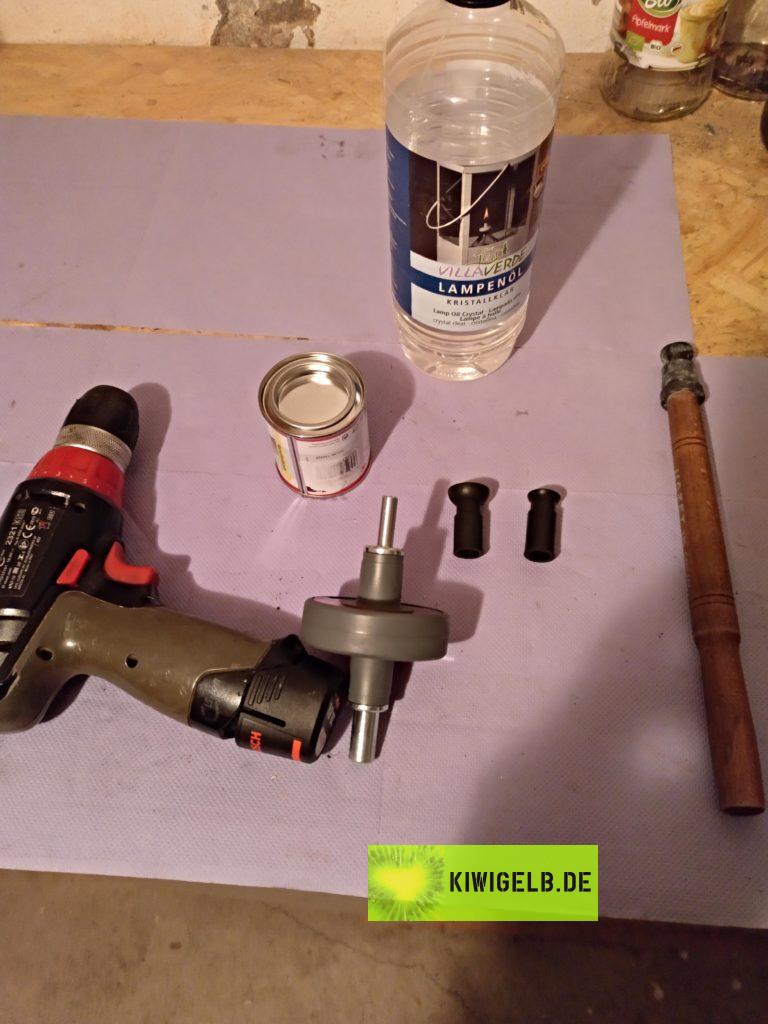
Das Ventileinschleifgerät setzt die Drehbewegung vom Akkuschrauber in eine links/rechts Drehbewegung um. Die Dose Schleifpaste enthält grobes und feines Schleifmittel und naja der Handschleifer war das Backup falls das Schleifgerät nichts taugt.
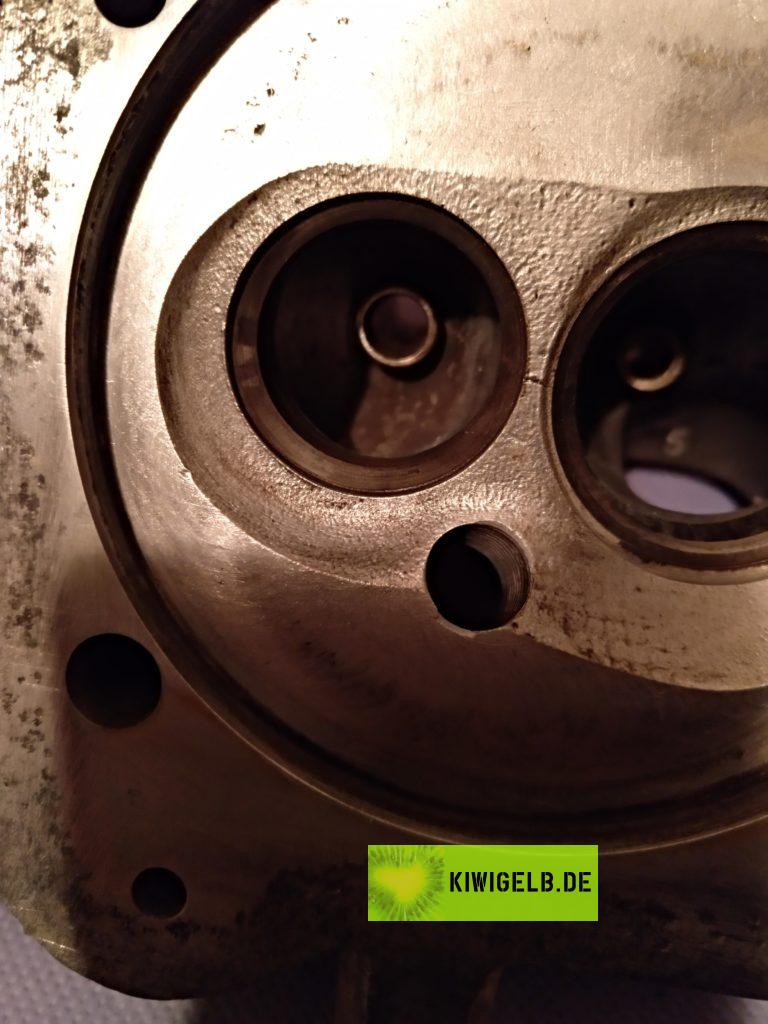
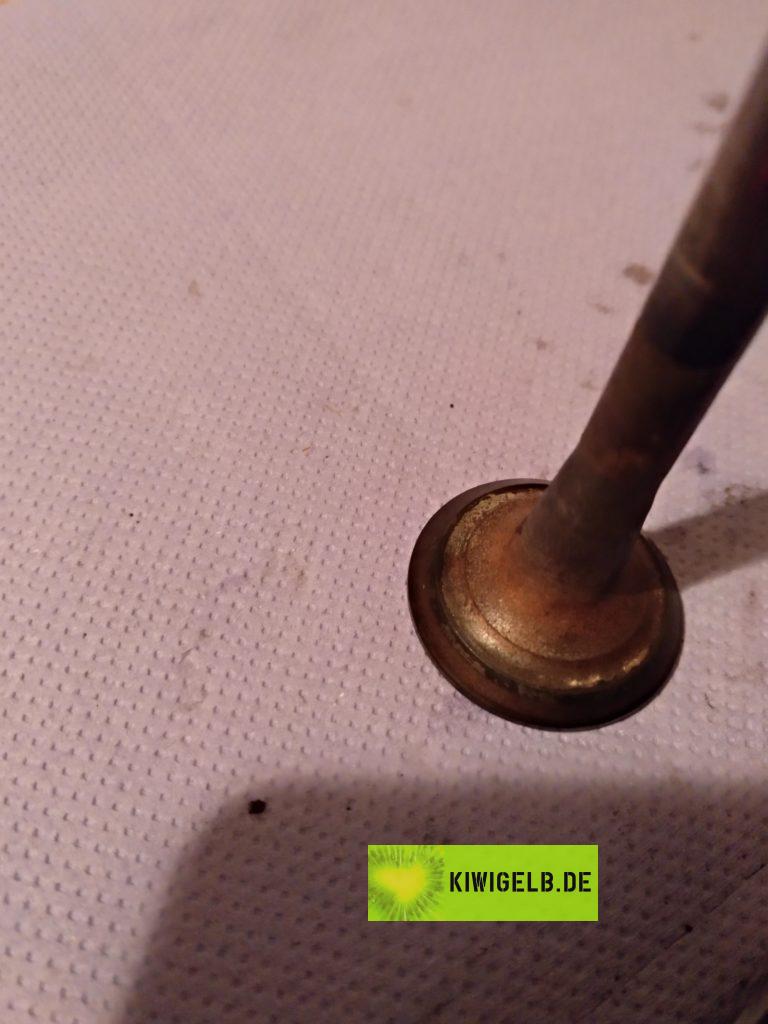
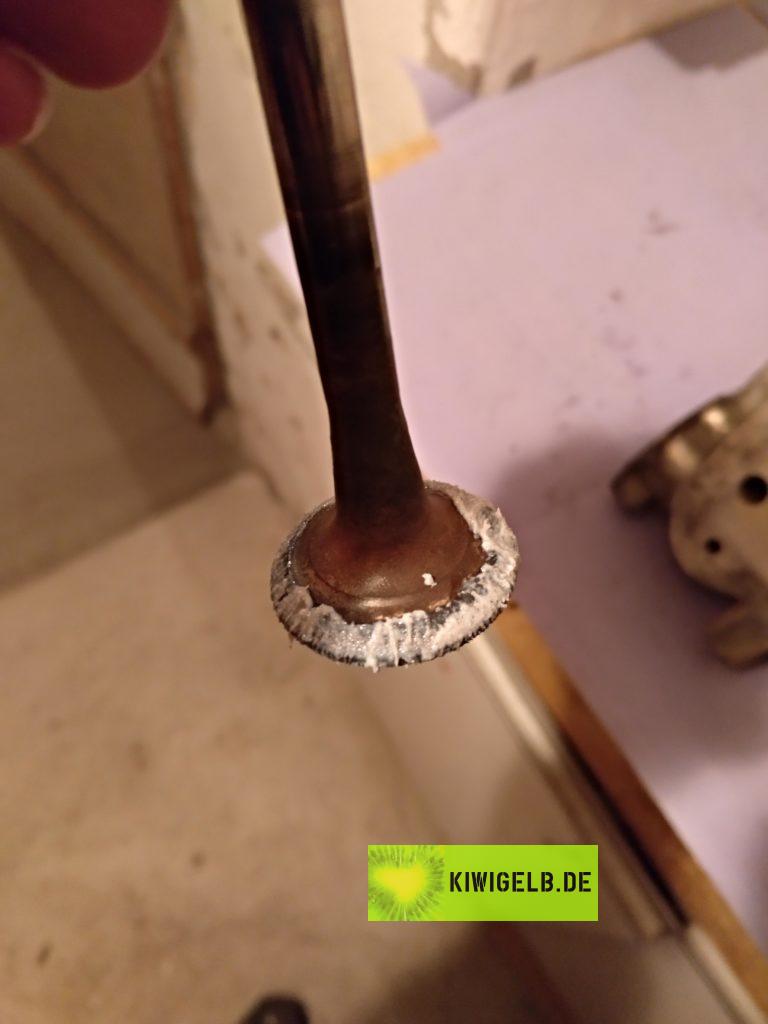
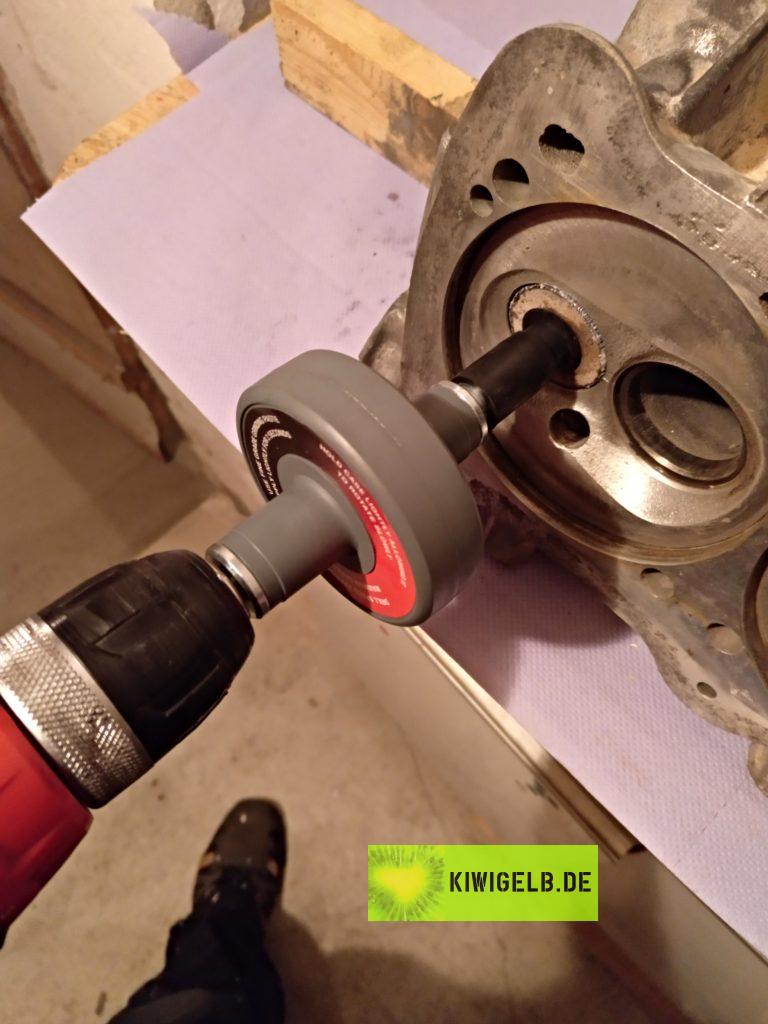
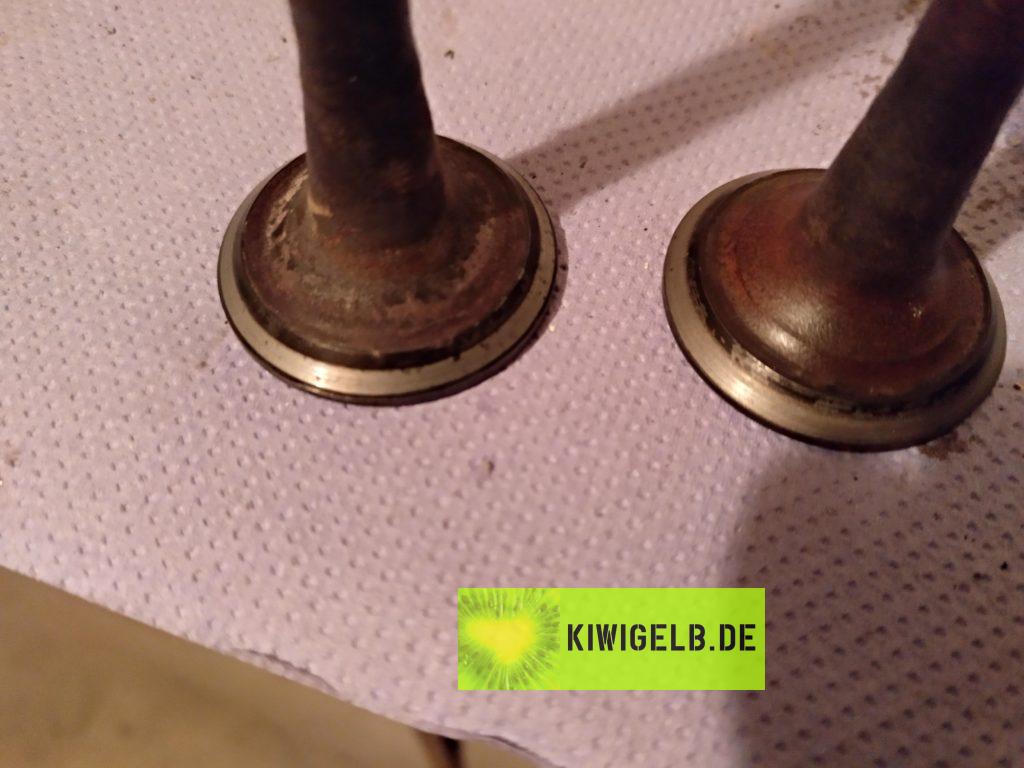
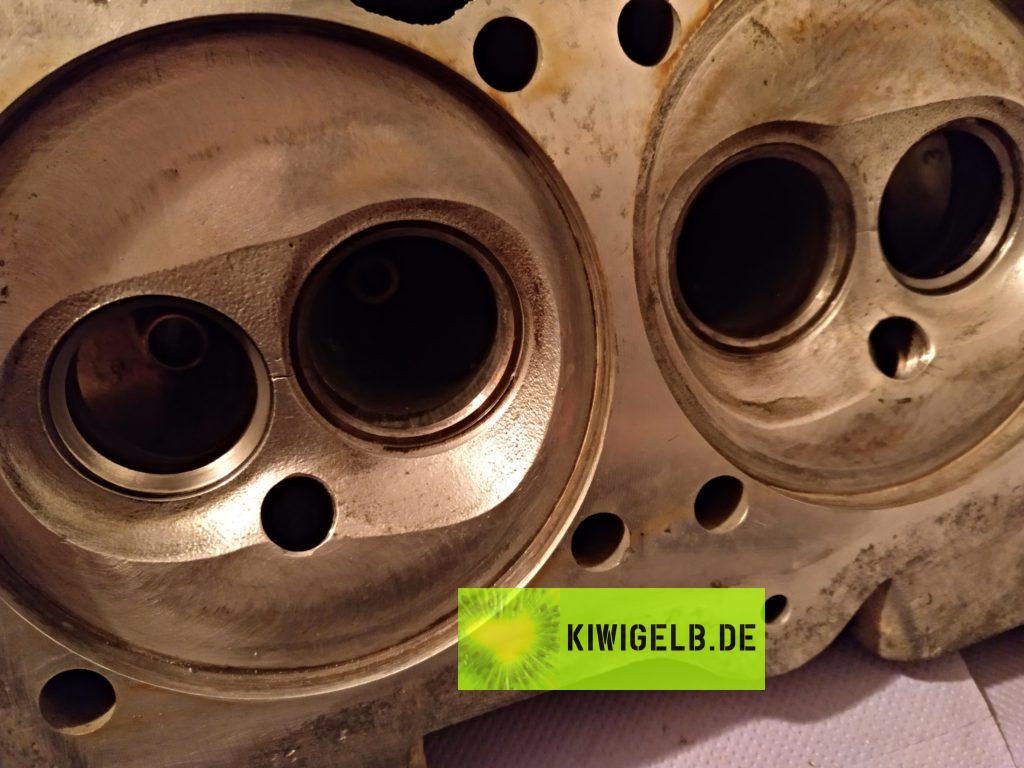
Nun mussten die Ventilsitze gefräst werden, keine Arbeit für daheim bzw. ohne die passenden Maschinen.
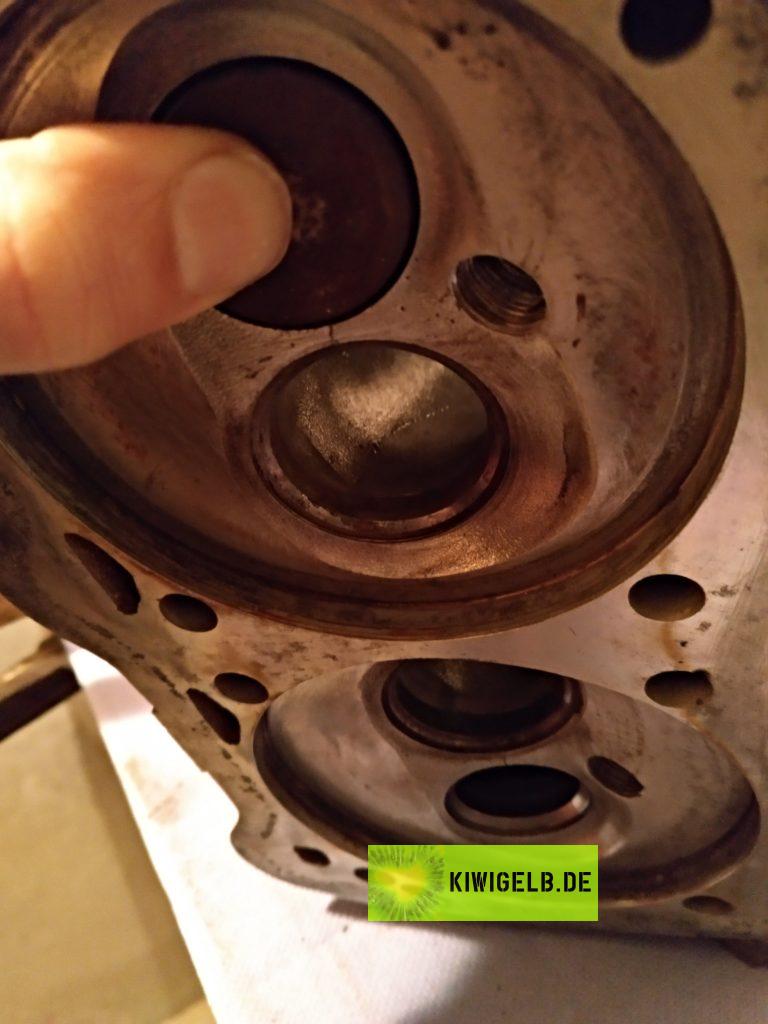
Hier mal die Ventilsitze nach dem Fräsen. Sehr schön erkennt man den schmaleren Bereich und auch die 3 verschieden Winkel auf dem Ventilsitz.
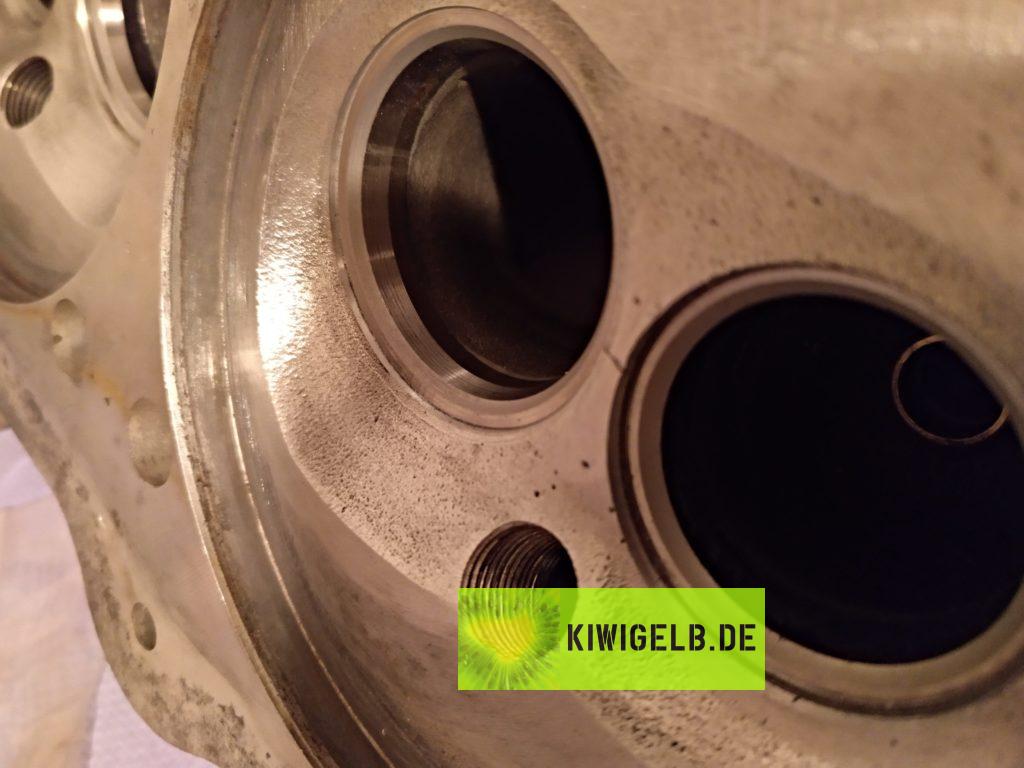
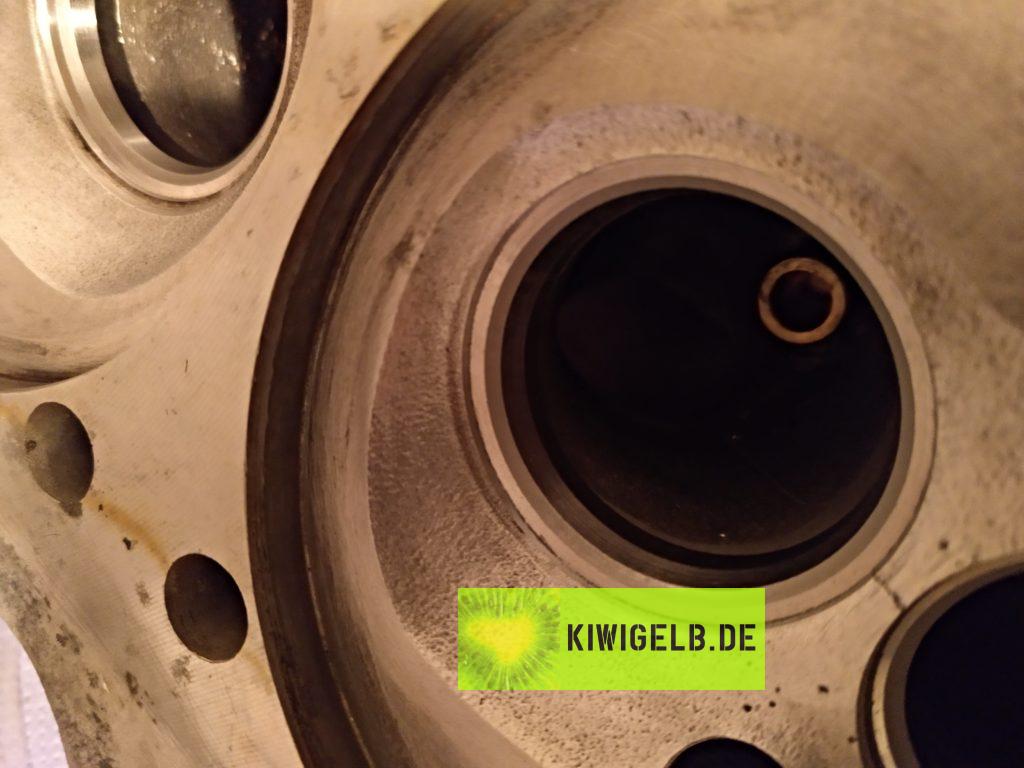
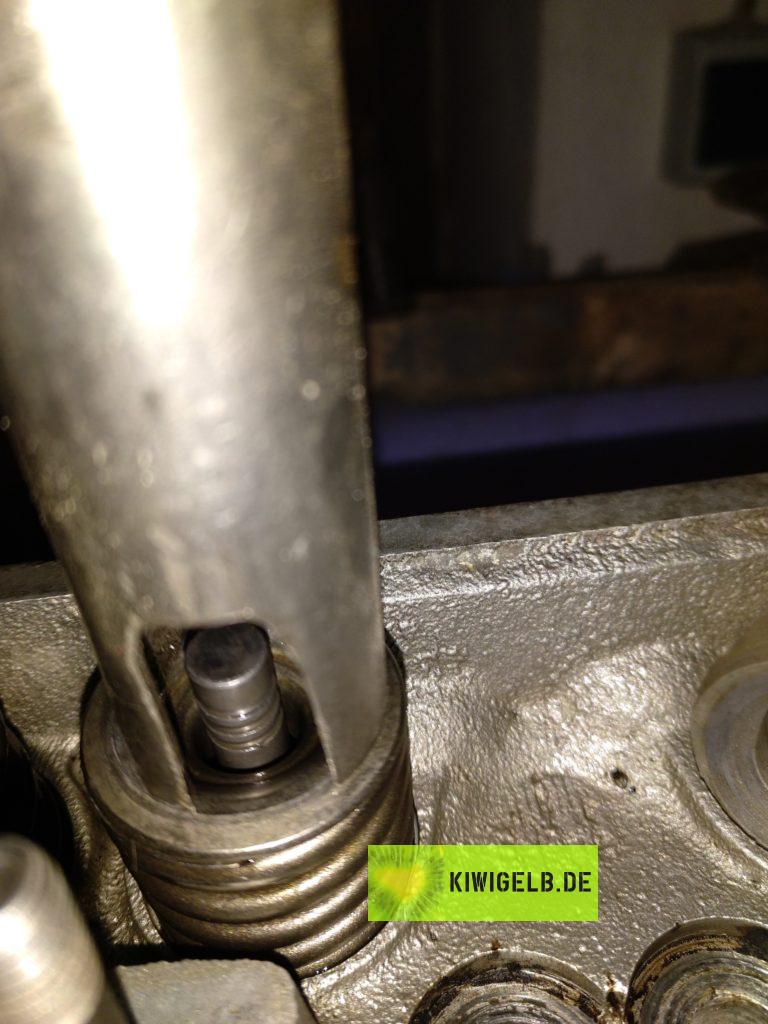
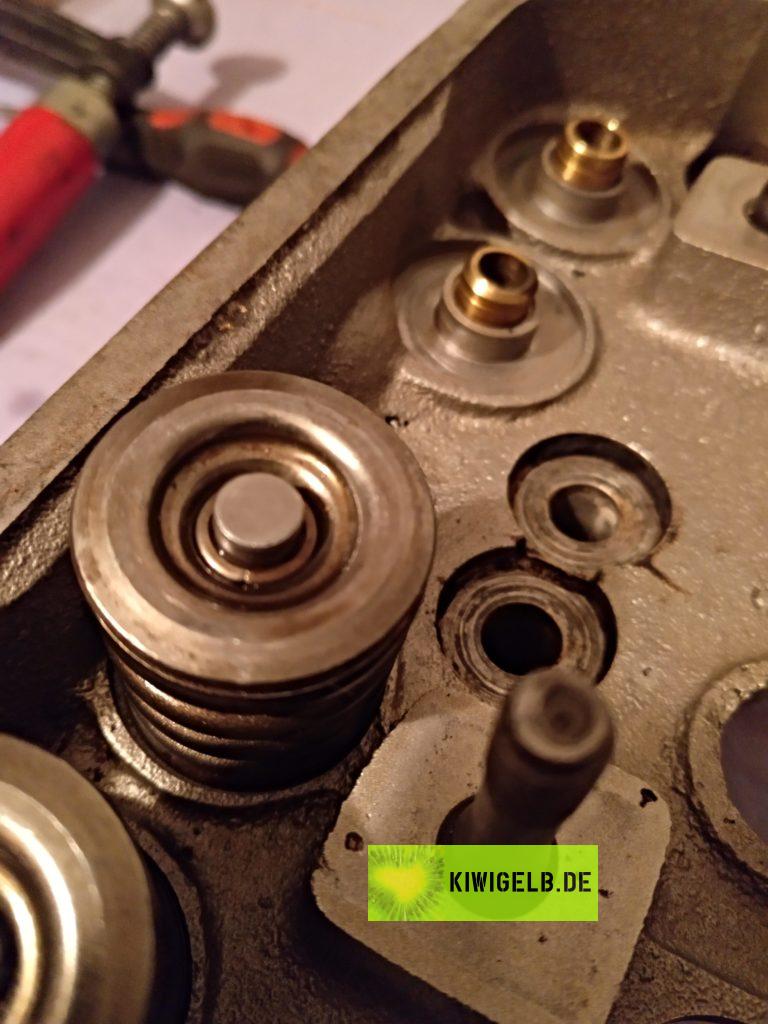
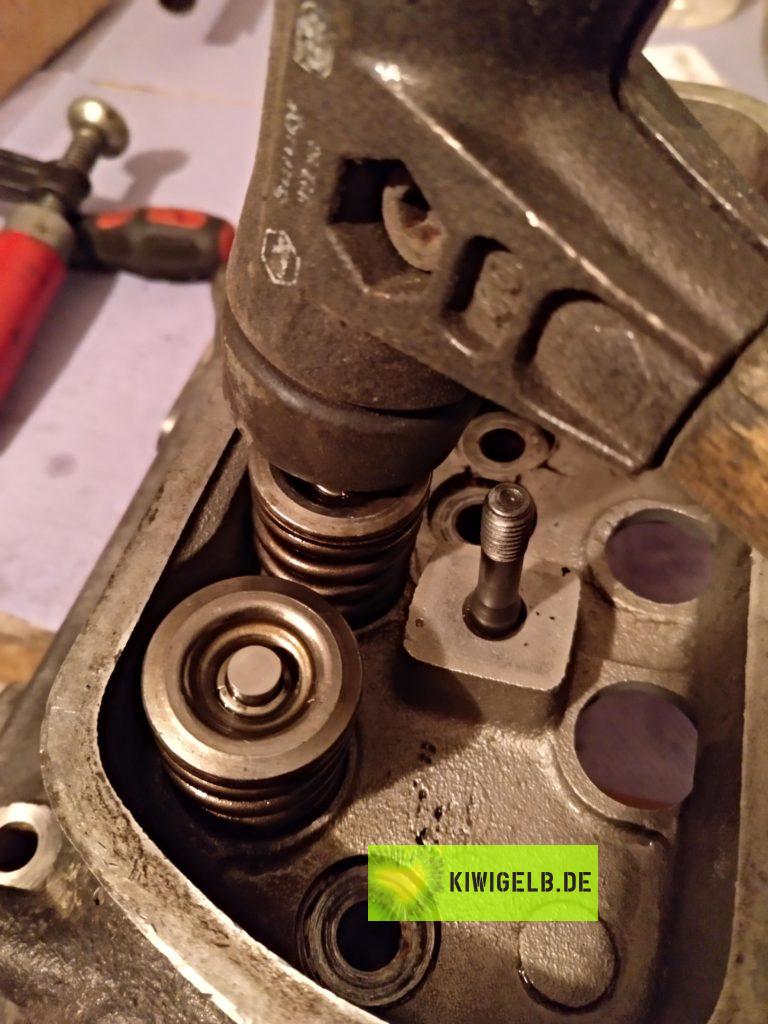
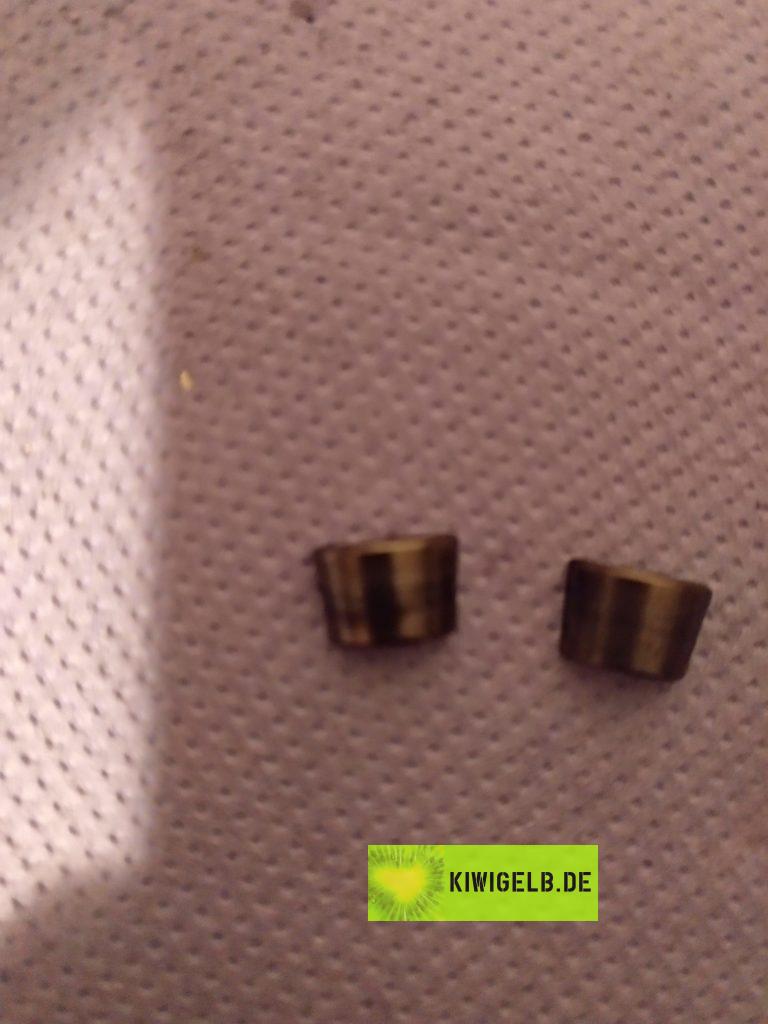